For Portage Plastics, SynergySPC Paid for Itself in the First Year
Executive Summary: Portage Plastics Corporation (PPC) is best known for being a thermoforming company. Thermoformed packaging components roll off the production lines by the thousands at Portage Plastics. The company can produce anything from instant cereal bowls to clamshell packing for windshield wiper blades to containers for baby wipes. For their largest customers, the production volume can total millions of units per year.
Case Study | Case Studies, Consumer Products, Food & Beverage, Industry, Outcome, Resources, ROI, Software, Synergy 2000
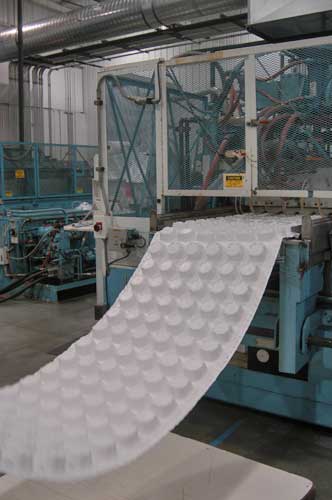
The Challenge
• Versatile product to collect Statistical Process Control (SPC) dataThe Solution
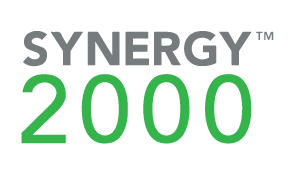
The Results
- Reduction in errors
- Product paid for itself in the first year
- Product returned rate has dropped to less than half a percent
The Details
Portage Plastics Corporation (PPC) is best known for being a thermoforming company. Thermoformed packaging components roll off the production lines by the thousands at Portage Plastics. The company can produce anything from instant cereal bowls to clamshell packing for windshield wiper blades to containers for baby wipes. For their largest customers, the production volume can total millions of units per year.
“Synergy paid for itself in the first year. Since using Synergy, our product returned rate has dropped to less than half a percent of what we are currently shipping.”
— Heidi Beaver, Quality Technician for Portage Plastics Corporation
Customers across the food, automotive, electronics, medical, personal care, agriculture, hardware and consumer industries respect the reputation at PPC to consistently meet their packaging applications and performance criteria. “Because every customer’s job is unique, I needed a program that would help me analyze the data in numerous ways regardless of the difference in our customers’ processes,” said Heidi Beaver, Quality Technician for PPC.
“The reason we selected the Synergy Statistical Process Control (SPC) software was because of its ease of use, because it was Windows-based software, and because it was an American-based company with a worldwide presence,” said Beaver. “One of the things I really appreciate about using Synergy is the personalized service I receive.”
This SPC software has greatly enhanced the company’s ability to pinpoint and react to adverse events that occur during production such as oven or heating issues, ambient temperature changes, material issues, trim press vibration, equipment maintenance issues or over-adjustments to machines. “The versatility in the query function gives me the exact data I need at any given time. Previously, I just looked at a 48-cavity run every 2 seconds as a whole: six rows across and eight deep,” explains Beaver. “Now I look at individual rows because we can get performance differences from the outside rows than we do from the inside rows. Therefore, I can immediately determine that the biggest shrink factor is affecting the outside rows, or know we have heating issues if we get thin sidewalls,” said Beaver.
“We have 2 sites using Synergy and since we implemented Synergy, we have seen a savings in man-hours and a huge reduction in errors,” said Beaver. “You can see the trending even as the shift progresses.” Previously, PPC would have to pull the product, sort the product, figure out what happened, pay 3 days of overtime, as well as repair the machine. “Synergy paid for itself in the first year,” said Beaver. “Since using Synergy, our product returned rate has dropped to less than half of a percent of what we are currently shipping.”
“Because of its real-time data, Synergy allows us to track, trend, and pinpoint specific areas,” said Beaver. “We can take preventative action versus being reactive. With the data from Synergy, everyone; from the operator, to the manager, to the engineer, can monitor an issue and resolve the issue before it adversely affects our customers.”
“In one instance, I noticed a potential problem going on. I was able to take that issue, retrieve 2 years of prior data, put the data in one file and chart it from there. I was able to query this information as well as having a chart. I was able to notify executive management and send them the data I had to back up the issue. I emailed them the information, we were able to have a meeting about it and resolve the potential problem before it became a problem for our customer,” said Beaver.
At their sister location in Brownsville, Texas, PPC has trained operators to take their own part measurements and enter the data directly into the software during second and third shifts. The location is staffed with a Quality Technician on duty for the day shift only. “Because everything is in real-time, I can go into their files, chart it and see for myself how they are running,” Beaver added.
“Previously when production was down, Portage Plastics would have to pull the product, sort the product, figure out what happened, pay 3 days of overtime, as well as repair the machine. Since using Synergy from Zontec, our product return rate has dropped to less than half of a percent of what we are currently shipping.”
— Heidi Beaver
Quality Technician for Portage Plastics Corporation