Grakon Selects Synergy 3000 for its Multi-Language Capability
Executive Summary: Grakon is a global leader in the design & development of advanced lighting systems & engineered trim components for premier OEM vehicle manufacturers. Grakon leverages best-in-class technology in the key areas of design, development, manufacturing and global distribution of vehicle lighting systems and engineered trim components. Our focus on leading technologies delivers value to our customers. For more information go to: www.grakon.com
Case Study | Automotive, Case Studies, Culture of Quality, Industry, Manufacturing, Outcome, Resources, Role, Software, Synergy 3000
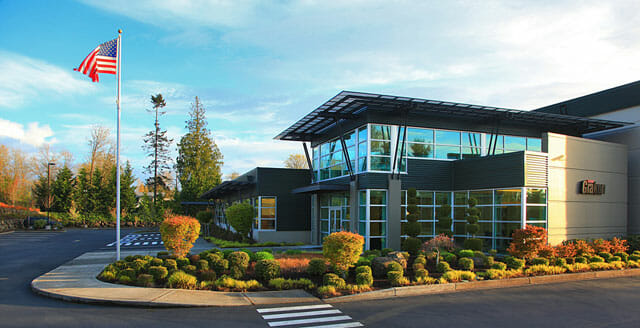
The Challenge
• Multi-language Statistical Process Control (SPC) software• Meet quality requirements
The Solution
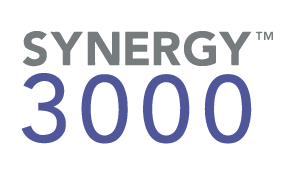
The Results
- Worldwide visibility into production process
- Improved quality system compliance and continuous improvement.
The Details
“We lacked a multi-language system that could easily be available throughout the company and the world so all the right people can see data live or almost live,” explained Don Bartlett, Director Quality & Customer Service for Grakon LLC. Grakon is a global leader in the design & development of advanced lighting systems & engineered trim components for premier OEM vehicle manufacturers. Grakon leverages best-in-class technology in the key areas of design, development, manufacturing and global distribution of vehicle lighting systems and engineered trim components. Our focus on leading technologies delivers value to our customers. “We provide lighting and engineered trim components for the commercial vehicle industry,” said Bartlett.
“We can have operators enter data in the plants across the globe, while engineers and managers can monitor the data anywhere in the world. Prior to implementing Synergy, we could not easily get this worldwide perspective, in particular from our plant in China.”
— Don Bartlett, Director Quality & Customer Service for Grakon LLC.
Since implementing Synergy, Grakon has realized immediate benefits. “We can have operators enter data in the plants across the globe, while engineers and managers can monitor the data anywhere in the world,” Bartlett said. ”Prior to implementing Synergy, we could not easily get this worldwide perspective, in particular from our plant in China.”
Bartlett explained that their customers require that all of their business be at least less than 50 Defective Parts Per Million (DPPM), some less than 15. This is close to the Six Sigma range. Grakon also follows Automotive Industry Action Group (AIAG) for capability requirements. “Typically, the standard is Cpk of 1.67, however, our internal goal is to be greater than 2,” Barlett said. “The Synergy Statistical Process Control (SPC) software has really helped us with quality system compliance, and continuous improvement.”
“The Synergy SPC software provides us visibility into our processes so that we have improved control and can be proactive vs. reactive to issues,” said Bartlett. This allows Grakon to make corrections during the process, versus after the final product has been completed.
“What differentiates Synergy from the other solutions on the market is that it is multi-language, web based, and user friendly,” said Bartlett. “That was vitally important for our business.”
Bartlett saw another benefit of going with Zontec. By the example of its owner, Warren Ha, Bartlett saw a company-wide commitment to customer service. “Warren Ha is one of the reasons we went with Zontec. His ownership and follow through to make Zontec a success with every customer was clear up front, and this is what has driven our success with Zontec,” said Bartlett.
“Typically, the standard is Cpk of 1.67; however, our internal goal is to be greater than 2. Synergy has really helped us with quality system compliance, and continuous improvement.”
— – Don Bartlett
Director Quality & Customer Service for Grakon LLC.