SPIROL International Corporation Uses Synergy to Fine-Tune Its Processes
Executive Summary: SPIROL International Corporation (SPIROL) is a leading manufacturer of a diverse line of engineered components for fastening and joining, including precision shims, coiled and slotted spring pins, solid pins, disc springs, alignment dowels and bushings, spacers, compression limiters, machined nuts, threaded inserts for plastics, pin and insert installation equipment, and vibratory parts feeders.
Case Study | Case Studies, Culture of Quality, Industry, Manufacturing, Metal Components, Outcome, Role, Software, Synergy 2000
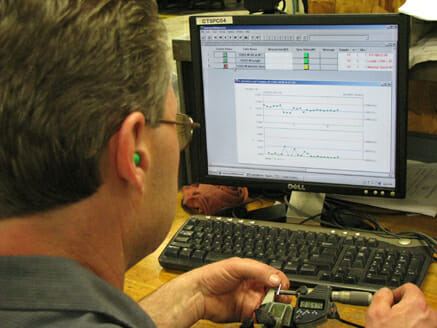
The Challenge
- SPC system that would capture and record data from start to finish
- A SPC system that would enable them to test out slight modifications before putting them into production
The Solution
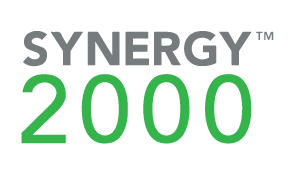
The Results
- Improve productivity and reduce variation in the finished product
- Capture more characteristics data without adding personnel
The Details
SPIROL International Corporation (SPIROL) is a leading manufacturer of a diverse line of engineered components for fastening and joining, including precision shims, coiled and slotted spring pins, solid pins, disc springs, alignment dowels and bushings, spacers, compression limiters, machined nuts, threaded inserts for plastics, pin and insert installation equipment, and vibratory parts feeders. “SPIROL is known for the development of metal fasteners, shims and installation equipment. SPIROL International was founded based on our invention of the coiled pin in 1948,” said Mike Woznicki, Quality Manager for SPIROL. “Where SPIROL started with one product (the coiled pin), we now manufacture over 2 billion components per year and supply companies all over the world through our global locations. Given the breadth of our product lines, our commitment to innovation and our approach to the market through Applications Engineering, SPIROL stands apart from all other companies in our industry.”
“We have over 110 pieces of equipment with over 22,000 items we monitor. We needed something that could capture this data instantly, enable our operators to monitor their processes across up to 6 machines and, if appropriate, take corrective action. We needed data immediately available that would monitor a process from start to finish that can involve up to 1 million pieces.”
— Mike Woznicki, Quality Manager for SPIROL
In 2009, SPIROL began looking for new Statistical Process Control (SPC) software. “We were using a hand-held Cpk calculator called Genesis. However, this did not provide us the immediate graphical display of the SPC data and historical data we needed,” said Woznicki. SPIROL selected the Synergy 2000 SPC software. “We have over 110 pieces of equipment with over 22,000 items we monitor. We needed something that could capture this data instantly, enable our operators to monitor their processes across up to 6 machines and, if appropriate, take corrective action. We needed data immediately available that would monitor a process from start to finish that can involve up to 1 million pieces.”
Because SPIROL operates in such high run at rates, for example, 500 pieces a minute, they wanted to ensure in advance that any changes they make in the process, that the overall quality is enhanced. “With Synergy, we have the ability to test out slight modifications in the production process, before we implement them on the shop floor, “Woznicki explained. “For example, we can experiment with what belt speed works best for our heat treating process based on the hardness readings related to temperature, time and speed of the belt. We learned from that process which belt speed gave us the optimal hardness that allowed us to increase productivity without sacrificing any characteristics of the part.”
SPIROL was also able to make changes in their phosphating rust prevention process. Based on the coating, they were statistically able to compare time and temperature with their salt spray results. “Now we are able to use the data we capture to make these continuous process changes in a controlled environment, before we make changes in production, “ Woznicki said. In order to maintain their position as being “the best” in the industry, SPIROL is constantly undergoing continuous improvement projects such as those mentioned above.
“Since implementing Synergy, we have increased productivity and concurrently reduced the variation in our end product,” Woznicki said. “Now operators have a graphical display that allows them to see if they are trending towards the upper or lower tolerances. They can immediately make adjustments. Also, we are now able to take more measurements in a shift by just a click of a button. We can see more of the process than we did in the past.”
Synergy has been instrumental in SPIROL’s audits as well. “We are able to show our customers in real-time that their product is “in control”, said Woznicki. “We bring every customer to an SPC station where they can view the data live. Without Synergy, we wouldn’t be able to do that. I use Synergy to demonstrate that our processes are in control.”
“With Synergy, we have the ability to test out slight modifications in the production process, before we implement them on the shop floor. For example, we can experiment with what belt speed works best for our heat treating process based on the hardness readings related to temperature, time and speed of the belt. We learned from that process which belt speed gave us the optimal hardness that allowed us to increase productivity without sacrificing any characteristics of the part.”
— Mike Woznicki
Quality Manager for SPIROL International