Synergy Helps TDK Manage 50% Increase in Production Without Adding Staff
Executive Summary: TDK Philippines Corporation is a manufacturer in the Philippines of MR (magnetoresistive) heads for hard disk drives.
Case Study | Case Studies, Efficiency, Industry, Machine Tools, Manufacturing, Outcome, Resources, Role, Software, Synergy 2000
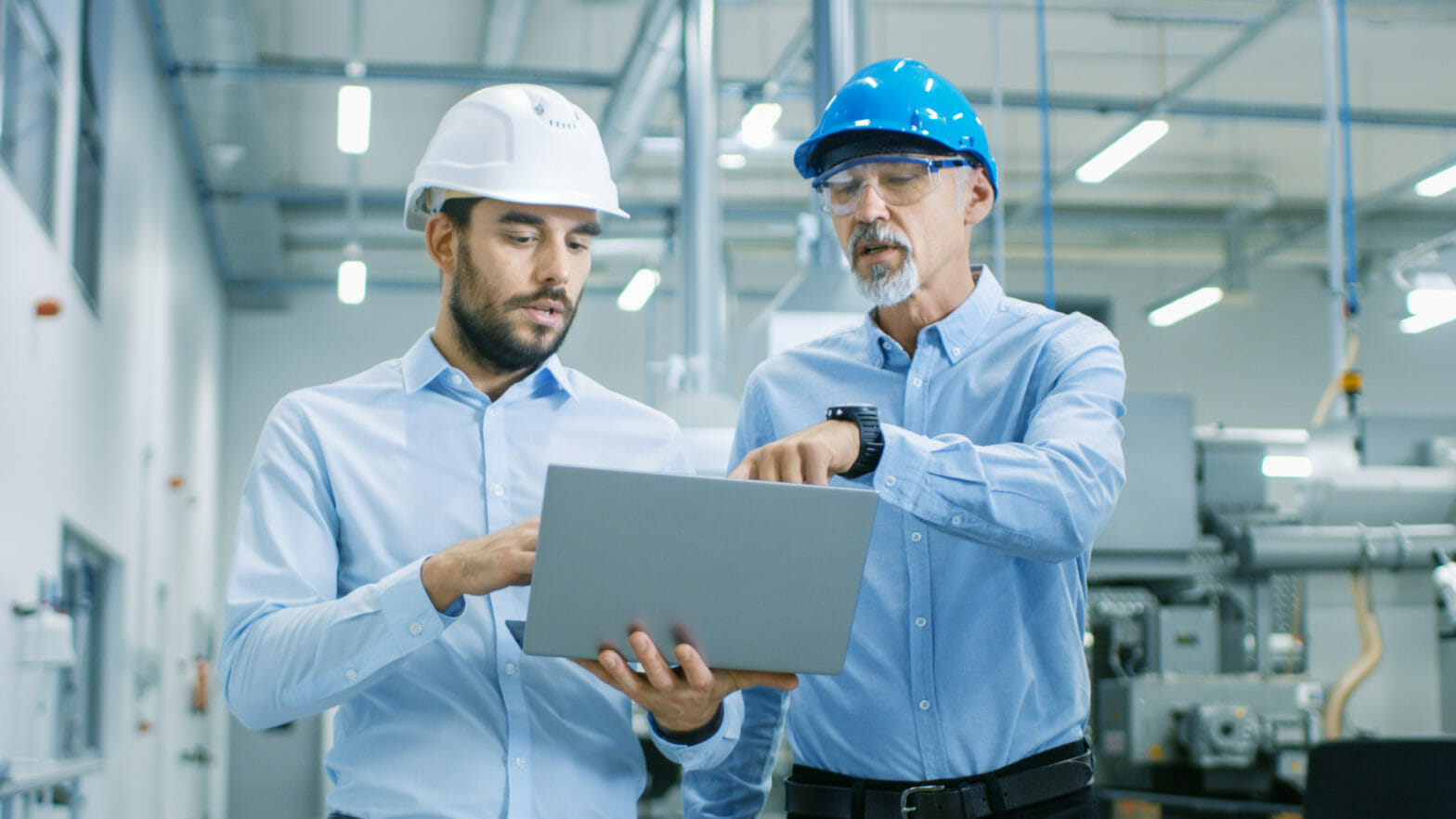
The Challenge
- Manual data entry
- SPC reporting via Excel
The Solution
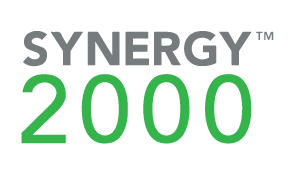
The Results
- Increase production by 50% without adding personnel
- Parameters increase by 300% without adding personnel
The Details
TDK Philippines Corporation (TDK) is a manufacturer in the Philippines of MR (magnetoresistive) heads for hard disk drives. “We strive to contribute to the growth of the Philippines and worldwide customers through our advanced manufacturing excellence,” said Alvin Hernandez, Sr. Manager for TDK.
In 2003, TDK began looking for a real-time SPC solution. “We were collecting and plotting all this data using Excel charts,” said Hernandez. “We had too many processes that were in need of monitoring. These processes involves too much data that manual crunching was not practical and requires too much time before the information could be made available to everyone. We had limited access on the process control chart.”
When deciding on a SPC solution, TDK selected the Synergy 2000 system. “We found the system to be very flexible. It shortens the time it takes to understand a problem compared in using Excel as we did in the past,” said Hernandez. With Synergy 2000, once the data is entered into the system it is instantly available in numerous SPC charts and reports.
“We selected Synergy 2000 because it is a true real-time SPC system. As we began using the product, we found that it provides a good interaction between operators, engineers and the management,” Hernandez said. Synergy 2000 is designed logically to meet the unique needs of the people that access the system, albeit operators, managers, or engineers. Each individual only has access to the parts of the system that they need to see to do their jobs. For example, operators only view the part of the system that is pertinent to entering data in to the system and monitoring if their process is out-of-control or out-of-specification. Engineers provide users permissions related to their view of the system as well as monitoring SPC analytics through various charts and reports available. The managers have a dashboard which provides them an instant, real-time perspective of how every process in the company is operating.
Once TDK implemented Synergy 2000, they were able to reduce errors and save man-hours due to decreased manual encoding. “Once we implemented Synergy 2000, we were able to utilize automated data gathering and timely data transfer.”
Since using Synergy, TDK has been able to enjoy increased production without adding personnel. “We have recently seen our volume increase significantly, and consequently the number of assembly lines increase by 50%,” said Hernandez.”Previously, we would have had to hire more operators to performs the critical parameter monitoring, especially since we apply control charts by machine and by parameters. This has become more critical because our number of parameters has also increased by 300%. Because we now use Synergy, our operators can perform multitasking, and we did not need to add additional operators to our assembly lines. Synergy actually contributed in our drive to improve production efficiency.”
Another area that Synergy 2000 has helped TDK is in the area of audits. “In every customer audit where they wanted to see how our SPC system works, Synergy is our showcase,” said Hernandez.
Synergy has also helped TDK meet its overall company objectives. “Synergy 2000 has helped us meet our customer requirements and produce high quality products,” concluded Hernandez.”It contributes to our goal towards achieving advanced manufacturing excellence.”
“We have recently seen our volume increase significantly, and consequently the number of assembly lines increase by 50%. Because we now use Synergy, our operators can perform multitasking, and we did not need to add additional operators to our assembly lines.”
— Alvin Hernandez,
Sr. Manager for TDK