Synergy SPC Software Vs. ERP Software
Executive Summary: Beginning in the early 80’s, we have been committed to developing the best SPC software in the world. Over 30 years, it has taken innovation, commitment, and listening to customers’ feedback. We have incorporated new ideas, suggestions, and new technologies into Synergy SPC software products. SPC software has to be easy-to-use, logical and well-engineered using cutting-edge technology. Today, we have delivered Synergy SPC software products that have fulfilled the goals we set from day one.
May 19, 2022 | Whitepapers | Resources, Whitepapers
Table of Contents
SPC Software
Synergy SPC software is a production based online real-time SPC system. It is easy to implement and easy to learn, requires very low maintenance and is reliable with little software downtimes. Production operators can input live data into the real-time system. Multiple concurrent users can utilize the system simultaneously to share and monitor live data during an online real-time production process. For example, if a process has an out-of-spec and/or out-of-control condition, the SPC software will automatically send real-time email to the appropriate personnel. Online, real-time SPC software allows process information to be immediately accessed by all levels of the company including management. We have seen our customers benefit from online real-time software time and time again.
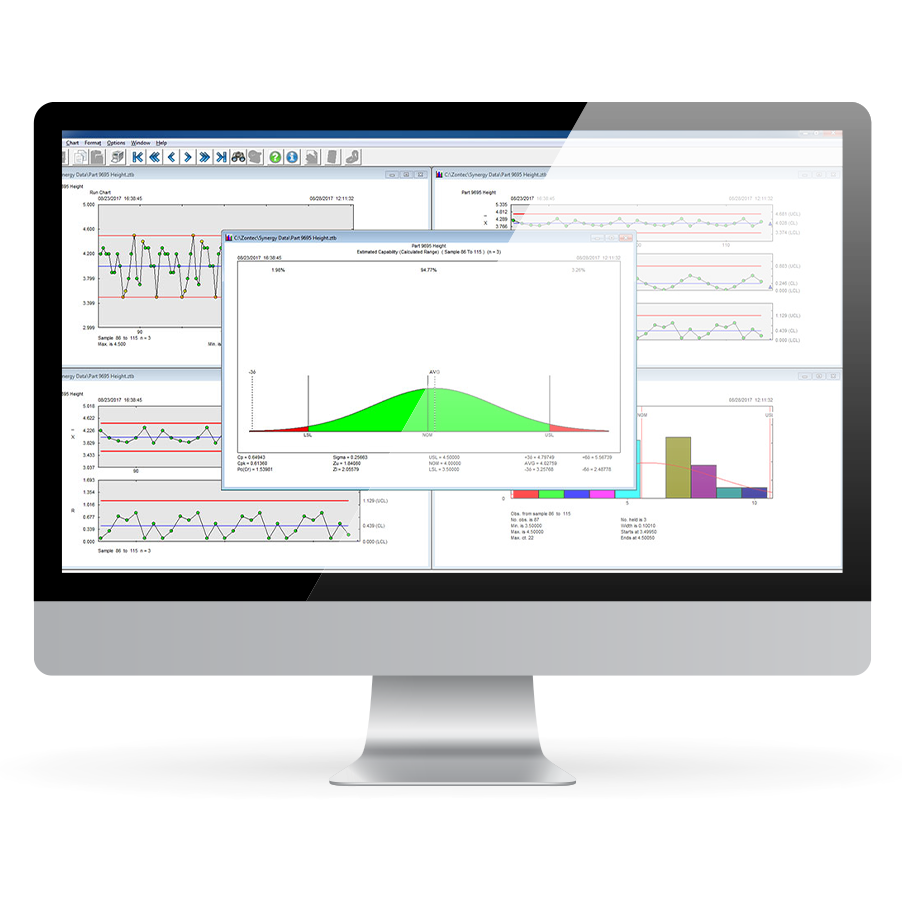
The SPC software offers numerous, easy to read charts. Available charts include a control chart, run chart, attribute chart, histogram chart, six sigma capability chart, box and whisker chart, gage R&R chart, multi-axis overlay chart, pare to chart and many others. Production floor personnel and management can communicate easily through comprehensive SPC reports generated by Synergy SPC software.
ERP Software System
Enterprise resource planning (ERP) is business management software that is usually a suite of integrated applications, that a company can use to collect, store, manage and interpret data from many business activities: product planning, cost, manufacturing or service delivery, marketing and sales, inventory management, shipping and payment.
Examples of ERP software systems are SAP, Plex, ProcessPro, Aptean, Sage ERP, Oracle JD Edwards, Microsoft Dynamics, Syspro, Epicor, QAD, IFS and many others. ERP systems are specialized to fit various business environments and company sizes. ERP systems can be specialized into discrete manufacturing, mixed mode and process manufacturing, industrial and wholesale distribution, and assembly and professional services just to list a few. As stated above, ERP solutions are made to fit corporations by business size and revenue. ERP systems can cost up to several million dollars, and implementations of these systems usually take years rather than months. There have been cases where the ERP implementation itself took so long that the companies involved were out-of-business before the implementation was complete.
SPC Methodologies and Rules
Often overlooked, the most critical and important component for an ERP quality module is that it correctly applies the SPC standards, methodologies and rules. Most individuals are unaware of this when they are evaluating the quality module of the ERP software. They trust that the ERP software vendors will incorporate the correct SPC rules into their quality module of the ERP software, which, in most cases isn’t true.
Some of the ERP systems offer quality modules in their software with very limited SPC functions. Often these SPC quality modules do not even comply with the correct SPC methodologies and rules. Corporate management would find it counterproductive to require its quality and production personnel to use an inadequate quality module instead of a robust, real-time SPC software on the production floor and in the quality labs. Incorrectly applied SPC methodologies will result in a loss of credibility, confidence, demoralize a team and negatively affect the corporation.
In a highly unpredictable and/or unstable production environment, companies lose tremendous amounts of money due to production errors, and untold hours trying to correctly assign the cause of these issues. If critical decision-making is made based on incorrect information, the tangible results are easily felt company-wide and the true causes of errors will remain unknown. Loss of trust in the accuracy of your data may result in strained relationships internally and with both customers and suppliers that translates into recalls, audits, penalties, and ultimately business losses.
SPC methodologies and rules takes years of complex programming knowledge, production experience, a commitment and a dedication to develop SPC software which performs properly. We know this because we did it with all of our Synergy SPC products. We have been implementing these SPC standards, methodologies, and rules correctly for 30 years.
Time Saving and Cost Justification
ERP vendors may be so firmly entrenched into an organization’s hierarchy; many companies already have a bias toward these familiar technology providers. They present cases that initially appear very comprehensive, offer one-stop shopping, interoperability and application manageability. With increased frequency, these issues cloud the selection process and often overshadow the best tool for the job. Corporate management has devoted all of its resources, financial and otherwise, to implementing an ERP system. In the meantime, quality improvements are delayed indefinitely; production and quality personnel become overly frustrated, defects, scrap, and rework occur more frequently and are rationalized as a “cost of doing business”. These costs are real and can easily multiply due to the time to rework and/or to reproduce the product.
Synergy SPC software products are reasonably priced and can truly provide value to your process and assist your improvement efforts now and in the future. Most importantly, our Synergy SPC software applies the 100% correct SPC methodology and rules. The SPC software implementation could be done in less than a week with minimal IT involvement. The ROI is achieved in approximately two to three months and you can enjoy the benefits of online real-time SPC capabilities. By utilizing sound SPC software, continuous improvement naturally leads to steady improvements despite limited resources. Synergy SPC software has the capability to integrate with your ERP system and incorporate business data into the SPC software after the ERP system is fully integrated.
Factory Automation and Device Integration
One other element that is also vitally important for the SPC software, especially used in the manufacturing environment, is to integrate with gage devices and data collection equipment. To aid the production operator during data input with an electronic gauging device, SPC software contains device interface capability to automatically direct data into the software. The SPC software also has the ability to integrate with data collection equipment to bring the data directly into the SPC software as part of factory automation projects. This feature was developed by software engineers with many years of manufacturing experience with automation knowledge. The ERP software quality module does not offer this interface because they are primarily a business management system and lack factory automation expertise.
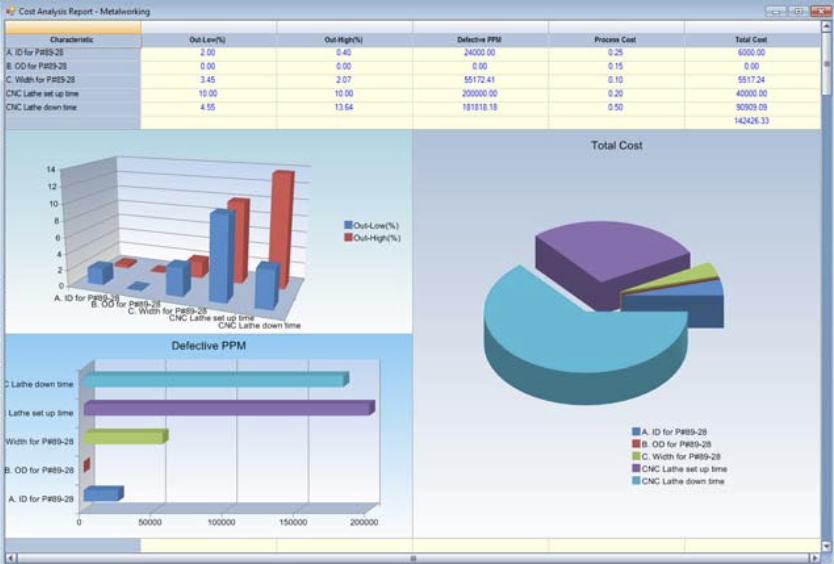
Synergy SPC Software vs. ERP Software
SPC software and ERP software quality modules are not alike. In terms of functionality, ERP quality modules generally incorrectly apply SPC methodologies and rules, have limited SPC capabilities, and contain a cumbersome user interface. Since many quality modules lack the depth of functionality in a best-of-breed SPC system, they have inadequate chart graphics, inflexible SPC functions and access only to aged production data for process feedback which makes the quality task difficult, if not impossible. It is vitally important to use the correct tool for the right application. Allow your quality and production personnel to first clearly define the application they need, evaluate the ERP quality module versus the best-of-breed of SPC software, set up an implementation plan, train users, measure results and make it a successful project. Then, if they want to integrate this online real-time SPC software with the ERP system once it is implemented, we can easily help you to do so.